Recent changes in diesel fuel have resulted in its shelf life decreasing, such as the introduction of bio and modern refining techniques. Consequently, problems like fuel contamination and tank corrosion are more frequent, so the demand for products and services like fuel polishing and tank cleaning has since increased.
Steel tanks are commonly used to store bulk amounts of fuel as they’re more robust than plastic tanks so are able to withstand bigger impact when onsite. They’re also usually non-porous, so are unlikely to absorb any fuel.
But despite their compatible strengths, their properties also mean that they’re more prone to corrosion from weather, such as heat, condensation and UV light. Water often forms in tanks during the warmer months as a result of heat gain and evaporation. This causes a tank to breathe, resulting in water and bacterial microbial contamination formation.
Last year’s cold weather followed by a dry summer led to a 23% rise in callouts to issues of corrosion & contamination
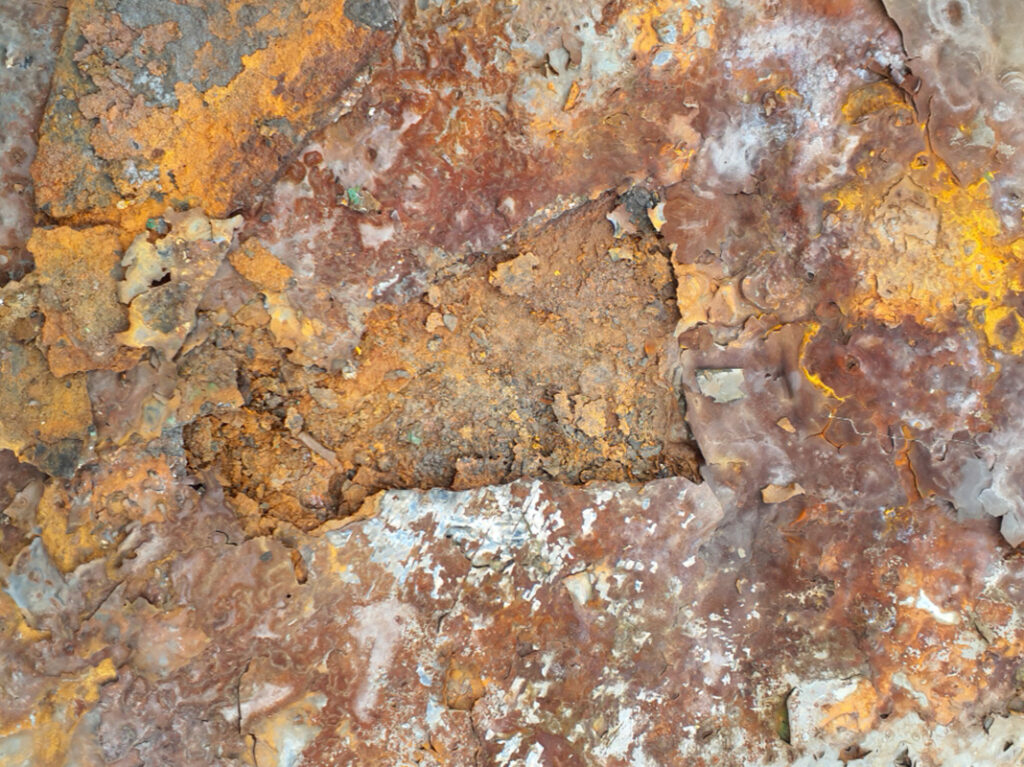
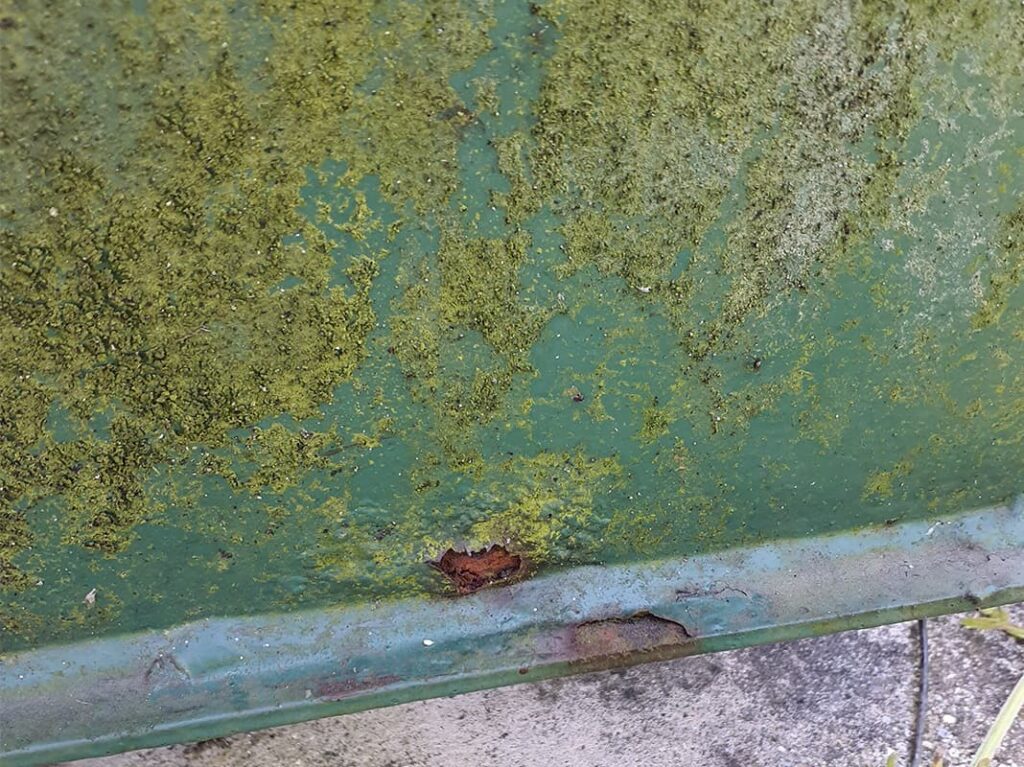
The oxidation of hydrocarbon ingredients increases when corrosion occurs, degrading the quality of the contents and leading to sludge build-up. This can:
- Reduce fuel lubrication
- Clog filters
- Obstruct the operation of release detection
- Eventually lead to equipment and machinery failure
There are 4 types of corrosion
- Pitting corrosion – found along horizontal surfaces, the bottom of tanks and where water builds up. Once it becomes thicker than one-third of the wall depth, that’s when external problems occur
- Weld metal corrosion – happens when metal interacts with metal in the fuel tank, causing an electrolytic action
- General corrosion – occurs anywhere in a tank
- Local corrosion – occurs in areas where water collects or flows
62% of equipment failure is caused by corrosion of tanks & a build-up of bacteria e.g. fuel algae and sludge
How can corrosion be detected?
It’s important to get fuel and tanks checked every six months. As corrosion forms from the inside of a tank, it’s not visible by exterior examination meaning further internal testing is needed.
Internal testing must be done by experts who have confined space entry training to ensure health and safety at all times. They do this by firstly removing the contents of the tank – known as a fuel uplift. The next step is a full internal clean down by using pressure jetting to get rid of any lose metal exposing any pitted or rusted areas.
This must then be checked by Non-Destructive Testing (NDT) to test the metal thickness at several areas of the tank and also the associated pipework if above ground. This is to look explicitly at the base plate as it is not visible unless the tank is cleaned – NDT is the only method to see the current health status of a tank. It uses measurement techniques to pinpoint any damage and anomalies in the fuel stored.
Tank thickness can vary between 6-12mm, depending on the size of the tank or site specification. For example, nuclear sites are at the larger end of thickness, whereas tanks in smaller commercial businesses are at the lower end.
So how can we prevent corrosion?
Small amounts of corrosion are inevitable due to the nature of the products stored, however there are several techniques and materials that can be implemented to prevent it. Most importantly, a proactive over a reactive approach must be applied to maintain fuel quality and to prevent operations downtime.
Last year, 75% of 482 callouts could have been avoided by regular checks & keeping tanks full to avoid the risk of moisture
Store fuel in a double skinned tank
A double skin on a tank provides twice as much protection from fluctuating temperatures and damage from impact. It offers leak detection and acts as a safety net to prevent leakage. A double skin ensures the fuel tank is contained within a vacuum to prevent corrosion as there’s no risk of moisture or air getting in.
According to the Environmental Agency, between 2002 and 2005, there were approximately 180 fuel spills, with 27% caused by leaks from tanks
Apply a paint coating to tanks
Using a corrosion-resistant finish such as Hammerite Direct to Rust Metal Paint will protect the tank for much longer by repelling water and preventing rust from forming underneath.
Install a secondary containment
A bund (secondary containment) made of concrete or brick is legally required to contain and prevent spillages that can happen as a result of tank penetration. It must be able to hold 110% of its contents, so if there’s a leak, it’s overfilled or water forms in the tank, the outer bund can fully contain it safely.
Install a valve and bung
A drawback of an outside bund is that they are exposed to natural elements so will likely become full of rainwater, which can over time build up and cause oil to escape by surpassing the bund wall. It’s vital that robust measures are implemented to extract rainwater from exposed bunds, such as through a valve. This must be kept shut at all times but can be opened to remove any uncontaminated water from within.
Another method to avoid leakage is to tank dewater at outlet pipes, for example a bung. This will detect liquid interfaces between oil and water. It should be fitted ¼ inch from the bottom of the tank to provide a means for water to escape and keep the oil contained. Tanks must be dewatered every six months to stop water build-up leading to corrosion.
Fuel analysis
Contamination must be detected early on so you can source, diagnose and repair any issues found. That’s why every six months is recommended, so a proactive rather than reactive approach can be taken. Once fuel has been contaminated already, it’s more likely that it will become contaminated again as it’s stability decreases. Regularly checking and testing the condition of your fuel to monitor any recurrences of contaminants will enable you to act quickly.
Fuel analysis assesses water, FAME and sulphur content, viscosity, density and the level of microbial contamination. Contamination can cause big problems with your machinery or equipment’s internal compartments, damaging them beyond repair or even worse, bringing operations to a halt.
Fuel polishing
Fuel analysis will determine the level of contamination present. If not too badly degraded in quality, fuel polishing can be carried out. This is an intensive process that involves removing the contaminated fuel through two stages to removed water, sediment and microbial contamination. The first step is filtration which is then followed by depolymerisation, which breaks down particulates and polishes the fuel to as good as new.
If the polished fuel remains in the same tank, the process can be less effective since fuel polishing only restores the fuel itself. The tank’s exposure to contaminated fuel will have caused microbial growth lining in the tank, resulting in the newly polished fuel becoming re-contaminated and you being right back where you were.
With that in mind, fuel polishing alone may not be truly effective, with the need to utilise additional services highlighted, particularly for those businesses who rely solely on backup power.
Tank cleaning
Tank cleaning requires the fuel to be drained from the tank so it can be cleaned and disinfected. Industrial vacuums are usually used to remove microbial growth, sludge and heavy sediment build-up that accumulate at the bottom of the tank, walls and struts.
The contaminated fuel that was removed can then be polished and pumped back into the clean tank or the contaminated fuel disposed of if too badly degraded.
Keep fuel tanks topped up
Keeping fuel tanks full, particularly during the summer months means there’s less space for air and therefore less chance of humidity and condensation.
Case study
A few months ago, we visited a university that had four small fuel tanks which each powered four separate backup generators. The tanks were only forty-percent full of fuel, and after an initial oil test, it was evident that the empty space had caused a significant amount of condensation and water to build up.
Due to the fuel being hydrolysed (spoiled with water), there’s an increased likelihood of internal corrosion and even worse, equipment failure when it’s needed more than ever.
Crown Oil Environmental engineers carried out a fuel uplift and fuel polish, followed by a man-entry tank clean, which discovered a large amount of internal corrosion in the dead-legs as a result of the fuel being sat dormant. This meant that the fuel tank had to be replaced. If the clean fuel was put back into the corroded tank, it would have simply contaminated the fuel again.
To find out more about any of our services, please get in touch on 0330 123 3399. Don’t let contaminated fuel and corroded fuel tanks affect your operations.
